The aim of a corrugator is to sell corrugated board packaging to his customers. He produces corrugated board sheets on a corrugator line (also called corrugator) and converts boards to Regular Slotted Cases (RSC) or more complex packaging. A corrugator can also directly sell sheets to converters.
Papers
To produce the corrugated cardboard, a corrugator orders paper rolls from a paper-maker. The rolls are delivered in widths that may range from 1750 mm to 3300 mm. There are different sorts of papers, including the following:
- Kraftliner: a paper used for liners, mainly made of new fibres. It’s the most resistant and the most expensive.
- Testliner: a paper used for liners, mainly made of recycled fibres.
- Chemi-mechanical: the most resistant fluting paper.
- Wellenstoff: a fluting paper, mainly made of recycled fibres.
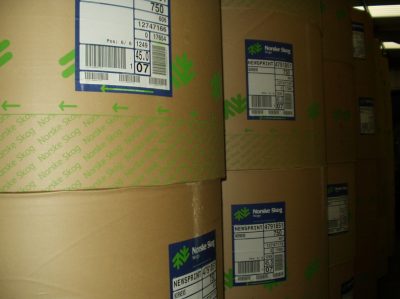
Paper roll
Manufacturing corrugated cardboard.
The corrugated cardboard is made on a corrugated line, namely a machine of more than 100 meters in length and 2.50 in width. The corrugator line consists of several elements:
- Two single facers: their role is to assemble a liner with a fluting paper. The fluting paper is hot corrugated in fluted rollers. There are different sizes of fluted rollers, which give the simple face different thicknesses. Examples: A-flute (Large, ~4.5 mm), C-flute (Middle, ~3.5 to 4.5 mm), B-flute (Small, ~2.5 to 3.5 mm) , E-flute (Micro, ~1.5 to 2 mm), K-flute or D-flute (Very large, more than 7 mm). Gluing the liner together with the fluting paper is achieved with a starch-based adhesive.
- There may be a third single facer if the corrugator line can produce triple wall. There are even quadruple wall corrugators.
- The double gluer, or double facer, where both single faces are assembled with the liner in order to achieve a double wall “double-double”.
- The hot plate: its purpose is to dry the glue. Out of the machine, the cardboard is hard.
- The slitter/scorer: it performs die-cutting and creasing of the cardboard sheets, according to the scheduled program and production order. The knives cut the cardboard sheet in secondary sheets; they also cut the trim waste. The creasing (or scoring) tools creases the secondary sheets: thus, folding the flaps will be made easier later on.
- The cross cutters (sheeters): they cut the sheets along at the output of the corrugator. After being cut, the sheets are stacked on pallets.
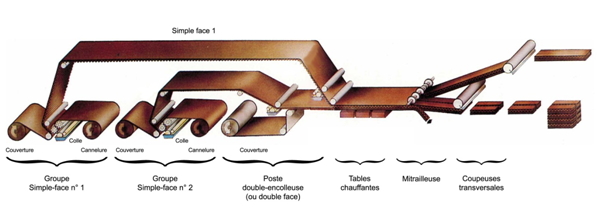
Schéma de fonctionnement d’un train onduleur
Corrugated cardboard sheets.
The produced cardboard sheets may have different “fluting profiles“. To describe a profile, we often use a code made of the association of flute codes (in this order: from the outer flute to the inner flute):
- Single face. A flexible element, not a sheet.
- Double face. Examples: A, C or B.
- Double wall or “Double-double“. Examples: EB or BC.
- Triple wall. Examples: BAK, BCA.
According to the fluting profile and the different papers used, there are different “board grades“. Fine-tuning the board grades is important to a corrugator. He must be able to certify a weight and many physical properties of the cardboard, such as: crushing, puncture, wet strength, etc. Internal laboratory controls are periodically carried on in this context.
Thus, a cardboard sheet is made of a board grade, with a certain size (“width” and “length“) and possibly scoring along.
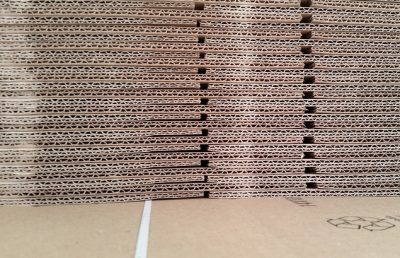
Corrugated board sheets
Manufacturing the packaging.
The corrugated boards get through a number of converting machines, in order to produce the packaging expected by the customer. The packaging can be simple, regular slotted cases (described in the FEFCO standard), complex, cut cases (CAO designs; required die-cuts) as well as POS made of several parts.
The different converting stages may include the following:
- The scoring machine: formatting or creasing.
- Printing: offset printing machine with coating units.
- Die-cutting: rotary cutting tool or flat-bed die-cutting machine.
- Folder-gluer: to fold and splice the boxes
- Strapping machine.
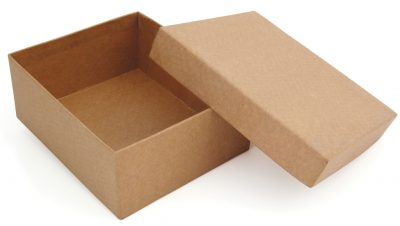
Corrugated cardboard case: a telescope cover box
Storage and logistics.
A good stock management by batch and location is an essential management component for the business of a corrugator. The logistics, allowing for better delivery rounds, is also a key factor.
Volume Software’s answer to the corrugators’ needs: VoluPack ERP.
VoluPack information system is specifically targeted at corrugators.